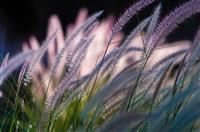
点击上方“机械设计非标菌”关注我们,每天学习一个机械设计相关知识点
阀体的铸造是阀门制造过程的重要环节,阀门铸件质量的好坏就决定了阀门质量的好坏。下面介绍阀门行业常用的几种铸造工艺方法:
砂型铸造:
阀门行业常用的砂型铸造,按粘结剂的不同还可分为:湿型砂、干型砂、水玻璃砂和呋喃树脂自硬砂等。
(1) 湿型砂是以膨润土为粘结剂的造型工艺方法。
它的特点是:造好的砂型不需要烘干,不需要经过硬化处理,砂型有一定的湿态强度,砂芯、型壳的退让性较好,便于铸件的清理落砂。造型生产效率高,生产周期短,材料成本低,便于组织流水线生产。
它的缺点是:铸件易产生气孔、夹砂、粘砂等缺陷,铸件的质量尤其是内在质量不够理想。
铸钢件湿型砂的配比及性能表:
(2)干型砂是以粘土为粘结剂的造型工艺方法,稍加膨润土可以提高其湿强度。
它的特点是:砂型需要烘干,有良好的透气性,不易产生冲砂、粘砂、气孔等缺陷,铸件的内在质量较好。
它的缺点是:需要砂型烘干设备,生产的周期较长。
(3)水玻璃砂是以水玻璃为粘结剂的造型工艺方法,它的特点是:水玻璃遇CO2后有自动硬化的功能,可有气硬化法造型和造芯的各种优点,但存在型壳溃散性差,铸件清砂困难以及旧砂再生、回用率低的缺点。
水玻璃CO2硬化砂配比及性能表:
(4)呋喃树脂自硬砂造型是以呋喃树脂为粘结剂的铸造工艺方法,在常温下由于粘结剂在固化剂的作用下发生化学反应而固化型砂。它的特点是砂型不必烘干,这就缩短了生产周期,节约了能源。树脂型砂易于紧实、溃散性好,铸件的型砂易于清理,铸件尺寸精度高,表面光洁度好,可以大大提高铸件质量。它的缺点是:对于原砂的质量要求高,生产现场有轻微的刺激性气味,而且树脂的成本也较高。
呋喃树脂自硬砂混合料配比及混制工艺:
呋喃树脂自硬砂的混制工艺:树脂自硬砂最好采用连续式混砂机,将原砂、树脂、固化剂等依次加入、快速混合而成,随时混制、随时使用。
混制树脂砂时各种原料的加入顺序如下:
原砂+固化剂(对甲苯磺酸水溶液)-(120~180S)-树脂+硅烷-(60~90S)-出砂
(5)典型的砂型铸造生产流程:
精密铸造:
近年来,阀门厂家越来越注重铸件的外观质量和尺寸精度。因为良好的外观是市场的基本要求,也是作为机加工头道工序的定位基准。
阀门行业常用的精密铸造是溶模铸造,现简要介绍如下:
(1)溶模铸造的两种工艺方法:
①采用低温蜡基模料(硬脂酸+石蜡)、低压注蜡、水玻璃型壳、热水脱蜡、大气熔炼浇注工艺,主要用于质量要求一般的碳素钢和低合金钢铸件,铸件尺寸精度可达国家标准CT7~9级。
②采用中温树脂基模料、高压注蜡、硅溶胶模壳、蒸汽脱蜡、快速大气或真空熔炼浇注工艺,铸件尺寸精度可达CT4~6级的精密铸件。
(2)溶模铸造典型工艺流程:
(3)溶模铸造的特点:
①铸件尺寸精度高,表面光整、外观质量好。
②可以铸造结构形状复杂、难以用其他工艺方法实现加工的零件。
③铸件材料不受限制,各种合金材料如:碳素钢、不锈钢、合金钢、铝合金、高温合金、以及贵重金属等材料,尤其是难以用锻造、焊接和切削加工的合金材料。
④生产灵活性好,适应性强。可以大批生产,也适用于单件或小批生产。
⑤溶模铸造也有一定的局限性,如:工艺流程繁琐、生产周期长。由于其可采用的铸造工艺手段有限,用于铸造承压薄壳阀门铸件时,其承压能力不能很高。
铸造缺陷的分析
任何的铸件内部都是会有缺陷的,这些缺陷的存在给铸件的内在质量带来很大的隐患,在生产过程中为消除这些缺陷进行的焊补也会给生产流程带来很大的负担。尤其是阀门作为承受压力、温度的薄壳铸件,其内部的组织致密性非常重要。因此,铸件的内部缺陷成为影响铸件质量的决定因素。
阀门铸件的内部缺陷主要有气孔、夹渣、缩松和裂纹等。
(1)气孔:气孔由气体产生,孔洞表面光滑,产生在铸件内部或近表面,形状多呈圆形或长圆形。
生成气孔的气体主要来源有:
①金属中溶解的氮、氢在铸件凝固的过程中被包容于金属之中,形成封闭的圆形或椭圆形内壁有金属光泽的气孔。
②造型材料中的水分或挥发物质都会因受热而变成气体,形成内壁为暗褐色的气孔。
③金属在浇注过程中,由于流动不稳定,将空气卷入而生成气孔。
气孔缺陷的防止方法:
①在冶炼方面应尽量少用或不用锈蚀的金属原料,工具和钢水包要烘烤干燥。
②钢水浇注要高温出炉、低温浇注,钢水要适当镇静以利于气体的上浮。
③浇冒口的工艺设计要增大钢水的压头,避免气体卷入,并设置人工气路,合理排气。
④造型材料要控制含水量、发气量,增加透气性,砂型和砂芯要尽量烘烤干燥。
(2)缩孔(松):它是产生在铸件内部的(尤其是在热节部位)呈连贯或不连贯的圆形或不规则的空洞(腔),内表面粗糙,颜色较暗,金属晶粒粗大,多呈树枝状结晶,聚集在一处或多处,水压试验时容易发生渗漏。
产生缩孔(松)的原因:金属由液态凝固为固态时发生体积收缩,此时如得不到足够的钢水补充,则必然产生缩孔。铸钢件的缩孔基本是由于对顺序凝固过程控制不当而造成的,原因可能有冒口设置不正确、钢水浇注温度过高,金属收缩量大等。
防止缩孔(松)产生的方法:①科学的设计铸件的浇注系统,使钢水实现顺序凝固,先凝固的部位应有钢水补充。②正确、合理的设置冒口、补贴、内外冷铁,确保顺序凝固。③在钢水浇注时,最后从冒口处顶注补浇有利于保证钢水温度和补缩,减少缩孔的产生。④在浇注速度方面,低速浇注比高速浇注有利于顺序凝固。⑸在浇注温度方面不宜过高,钢水高温出炉,经镇静后浇注,有利于减少缩孔。
(3)夹砂(渣):夹砂(渣)俗称砂眼,是在铸件的内部出现不连贯的圆形的或不规则的孔洞,孔内夹杂着型砂或钢渣,尺寸大小没有规律,聚集在一处或多处,往往在上型的部分较多。
产生夹砂(渣)的原因:夹渣是由于钢水在冶炼或浇注过程中,离散的钢渣随着钢水进入铸件形成的。夹砂是由于造型时型腔的紧实度不够,当钢水浇入型腔时,型砂被钢水冲起进入铸件内部造成的。另外修型、合箱时操作不当,有掉砂现象也是造成夹砂的原因。
防止夹砂(渣)产生的方法:①钢水冶炼时要尽量排气排渣彻底,钢水出炉后在钢水包里镇静一下,有利于钢渣的上浮。②钢水的浇注包尽量不用翻包,而用茶壶包或底注包,以免钢水上部的渣子顺着钢水进入铸件型腔。③在钢水浇注时要采取蓖渣措施,尽量减少钢渣随钢水进入型腔。④为了减少夹砂的可能,在造型时要保证砂型的紧实度,修型时注意不要掉砂,合箱前要将型腔吹干净。
(4)裂纹:铸件的裂纹大多为热裂纹,其形状不规则,有穿透或不穿透、连续或断续,裂纹处的金属呈暗色或有表面氧化。
产生裂纹的原因:有两个方面,即高温应力与液膜变形。
高温应力是钢水在高温下收缩变形受阻而形成的应力,当该应力超过了金属在该温度下的强度或塑性变形极限时便产生了裂纹。液膜变形是钢水在凝固结晶过程中晶粒之间产生液膜,随着凝固结晶的进行,液膜发生变形,变形量和变形速度超过一定极限时,便产生了裂纹。热裂纹产生的温度范围约在1200~1450℃左右。
产生裂纹的影响因素:
①钢中S、P元素是产生裂纹的有害因素,他们和铁的共晶物降低了铸钢在高温的强度和塑性,导致裂纹产生。
②钢中的夹渣和偏析增加了应力集中,因而增加了热裂倾向。
③钢种的线收缩系数越大,热裂的倾向越大。
④钢种的导热系数越大,表面张力越大,高温机械性能好,热裂的倾向越小。
⑤铸件的结构设计工艺性不好,如圆角太小、壁厚悬殊太大、应力集中严重,都会产生裂纹。
⑥砂型的紧实度太高,型芯的退让性不良阻碍铸件收缩会增加裂纹倾向。
⑦其它如浇冒口排列不当、铸件冷却速度太快、切割浇冒口及热处理造成过大应力等也都会影响裂纹的产生。
针对以上裂纹产生的原因和影响因素,采取对应的措施,就可以减少和避免裂纹缺陷的产生。
综合以上铸造缺陷产生原因的分析,查找存在的问题,采取相应的改进措施,就可以找到解决铸造缺陷的方法,有利于铸件质量的提高。
有问题请点击了解更多